Hysenetch (Xinhaisen) State-of-the-Art Etching Technology Empowers Medical Devices with Precision Engineering
In the era of rapid advancements in minimally invasive surgery (MIS) and implantable medical devices, the reliability of precision metal components directly impacts patient outcomes. As a critical microfabrication technique, photochemical etching plays an indispensable role in medical device manufacturing.
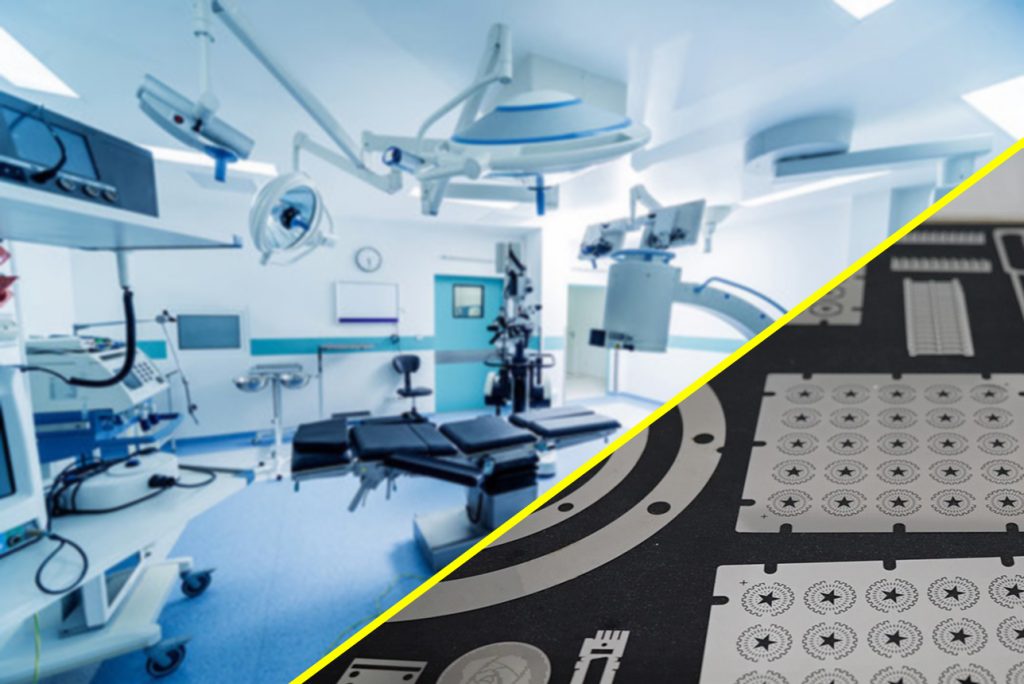
Leveraging our proprietary etching process, Hysenetch addresses the most challenging requirements for medical precision components. Our capabilities include:
Compliance with ISO 13485 and FDA regulations
Ultra-high precision tolerance of ±5μm
Minimum feature size as small as 10μm
Material thickness ranging from 10μm to 1mm
Customized solutions for global medical OEMs
Hysenetch can provide precision etching components for Medical Device
Hysenetch (Xinhaisen) provides customized precision machining solutions for global medical device manufacturers to ensure that each product meets the stringent requirements of the medical field. Currently, Hysenetch offers precision metal components, grids for X – ray machines, special surgical knife blades, blood and liquid filter components, precision implants, stents, pacemaker components, fascia plates, optical and electrical encoders, washers, shims, orthopedic pins, bone reconstruction components, vanes, chassis parts, gaskets, orifice plates, battery covers, clock second hands, grids, molecular sieves, optical elements, optics, mesh covers, etc. to the global medical device industry.